According to the preparation technology and application field of ceramics, ceramics can be divided into traditional ceramic materials and advanced ceramic materials. Advanced ceramics have gradually become an important part of new materials.
Advanced ceramics: according to chemical composition can be divided into oxide ceramics, nitride ceramics, carbide ceramics, boride ceramics, silicide ceramics, fluoride ceramics, sulfide ceramics, and so on. According to its properties and uses, it can be divided into two categories: energy ceramics and structural ceramics. Functional ceramics are mainly based on the special functions of materials, with electrical properties, magnetic properties, biological properties, thermal sensitivity, optical properties, and other characteristics, mainly including insulating and dielectric ceramics, ferroelectric ceramics, piezoelectric ceramics, semiconductor, and sensitive ceramics, etc. Structural ceramics are mainly based on the mechanical and structural uses of materials, with high strength, high hardness, high-temperature resistance, corrosion resistance, oxidation resistance, and other characteristics.
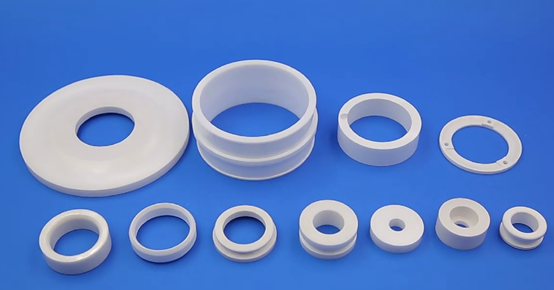
Structural ceramics with their excellent mechanical and thermal properties become an important branch of ceramic materials, accounting for about 30% of the whole ceramic market. In nearly 20 years, the national major projects and cutting-edge technology in ceramic material and its preparation technology is also put forward higher demands and challenges, such as aerospace rocket liquid hydrogen in liquid oxygen turbine pump use of silicon nitride ceramic bearings under the condition of low-temperature extremes no-slip condition at high speed, requirements at the beginning of the ceramic bearing high strength, good, wear resistance, surface processing of high precision; The large size ceramic sealing ring used in the main pump of nuclear power plant needs long service life and high reliability. In particular, the silicon carbide ceramic reflector used in the ground monitoring of the earth satellite shooting targets, in addition to high elastic modulus, low thermal expansion coefficient, and lightweight, requires high precision ultra-mirror and large size. This is a challenge to the molding technology, sintering technology, and processing technology of large-size structure ceramic materials. In optical communication, the inner hole of the optical fiber connector is 125 microns, and it requires a very high surface finish, dimensional accuracy, and concentricity. So Structural ceramics is the most promising quality material in an extreme environment.
For the oxide ceramics, nitride ceramics in structural ceramics, below is their feature:
Alumina ceramics: the earliest and most widely used structural ceramics
Zirconia ceramics: high-performance structural ceramics, toughening is the key to preparation
Beryllium oxide ceramics: oxide ceramics with the highest thermal conductivity,
Silicon nitride ceramics: one of the materials with the best comprehensive properties in advanced ceramics
Aluminum nitride ceramics: ideal structural material for microelectronics industry circuit board and packaging
Boron nitride ceramics: soft ceramics in ceramic materials, good machinability