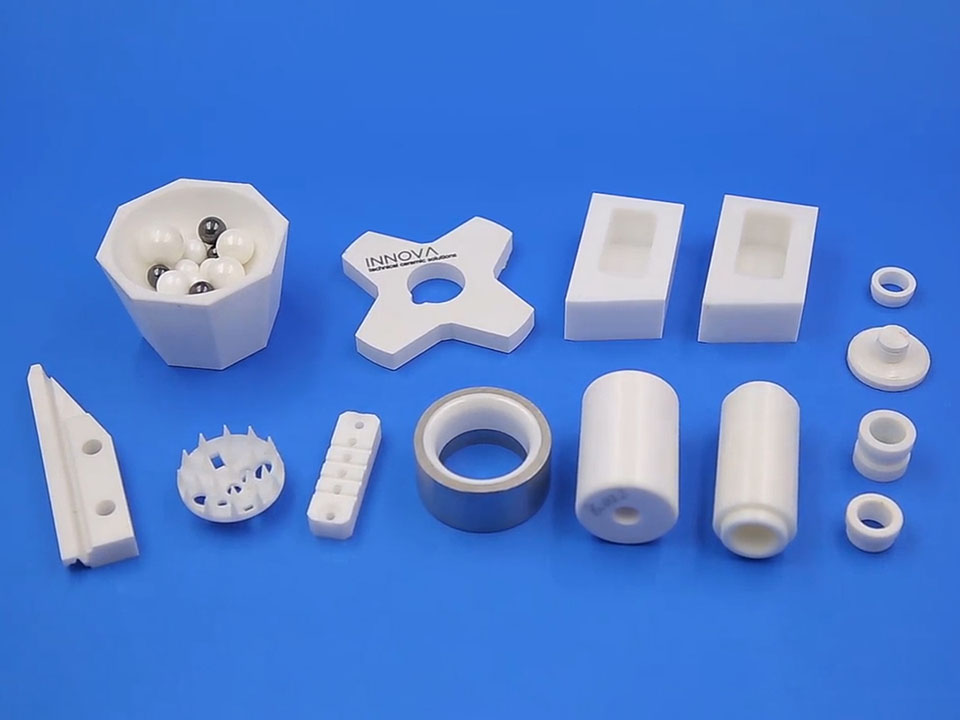
Compared with alumina ceramics, zirconia ceramics have more than three times the strength and can withstand high temperatures above 1000 degrees Celsius. The new materials promote the development of new applications in automobiles.
1. Application of Ceramics in Automobile Engines
To reduce the fuel consumption of diesel engines by more than 30%, it can be said that new ceramics are indispensable materials. The thermal efficiency of the diesel engine is 33%, which is very superior compared to the gasoline engine, but still, more than 60% of the thermal energy is lost. Therefore, in order to reduce this part of the loss, the combustion chamber is surrounded by ceramic materials with good thermal insulation performance for thermal insulation, and then the exhaust gas turbocharger and power turbine are used to recover the exhaust energy. Tests have proved that this can increase the thermal efficiency to 48%.
2. Application of Special Sensitive Ceramics in Automotive Sensors
The requirements for automotive sensors are that they can be used for a long time in the harsh environment unique to automobiles (high temperature, low temperature, vibration, acceleration, humidity, noise, exhaust gas), and should have the characteristics of small size and lightweight, good reusability, and wide output range. Ceramic heat resistance, corrosion resistance, wear resistance, and its potential excellent electromagnetic and optical properties have been fully utilized with the advancement of manufacturing technology in recent years, and sensors made of sensitive ceramic materials can fully meet the above requirements.
3. The application of ceramics in automotive brakes
Ceramic brakes are built on the basis of carbon fiber brakes. A carbon fiber brake disc is initially composed of carbon fiber and resin. It is pressed into shape by a machine, and then heated, carbonized, heated, and cooled to make a ceramic brake. The hardness of the carbon-silicon compound surface of the ceramic brake is close to that of a diamond. The inner carbon-fiber structure makes it strong and resistant to impact and corrosion, making the disc extremely wear-resistant. At present, this kind of technology is not only used in F1 racing cars but also involved in super civilian sports cars, such as Mercedes-Benz’s CL55 AMG.
4. The application of ceramics in automotive shock absorbers
The shock absorber of the car is an intelligent shock absorber successfully developed by comprehensively utilizing the sensitive ceramic positive piezoelectric effect, inverse piezoelectric effect, and electrostrictive effect. Due to the use of high-sensitivity ceramic components, the shock absorber has the function of identifying the road surface and self-adjusting, which can minimize the vibration of the car caused by the rough road surface.
5. Application of ceramic materials in automobile spraying technology
In recent years, ceramic thin film spraying technology, which is widely used in aerospace technology, has begun to be applied to automobiles. The advantages of this technology are good thermal insulation effect, high temperature and high-pressure resistance, mature technology, and stable quality. In order to achieve the goal of low heat dissipation, ceramic spraying can be applied to the engine combustion chamber components, such as zirconia sprayed on the top of the piston and zirconia sprayed on the cylinder liner. The engine after this treatment can reduce heat dissipation loss, reduce the weight of the engine itself, reduce the size of the engine, and reduce the fuel consumption.
If you have more interests, pls feel free to contact us.