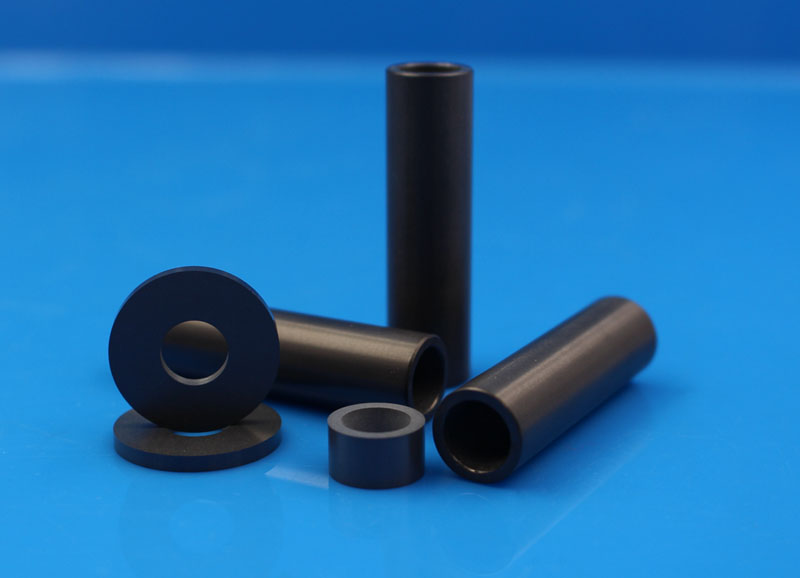
Silicon nitride ceramic has good properties such as high strength, high hardness, and high temperature resistance, and its hardness can reach HRA91~93; It has good thermal hardness and can withstand high temperatures of 1300~1400℃; It has a small chemical reaction with carbon and metal elements, resulting in its friction coefficient Low; It is self-lubricating which make it wear-resistant; It is strong corrosion resistance, except for hydrofluoric acid, it does not react with other inorganic acids, and has oxidation resistance at high temperatures; it also has good thermal shock resistance. It will not break even if it is rapidly cooled in the air and then heated rapidly; the high temperature creep of silicon nitride ceramics is small, and the slow plastic deformation produced under the action of high temperature and fixed load is small.
In addition, silicon nitride ceramics also have the advantages of high specific strength, high specific mode, high thermal conductivity, and excellent electrical properties. Therefore, it has special application value in extreme environments such as high temperature, high speed, and strong corrosive media. It is considered as one of the structural ceramic materials with development and application prospects. It is often the first choice in many applications that need to withstand the test. The following is an inventory of these application directions.
Regarding the application of silicon nitride, it first appeared in the 1950s, as the bonding of silicon carbide and oxide, corresponding to refractory materials, and then used to make crucibles, thermocouple tubes, rocket nozzles, etc. In the 1960s, as the demand for new materials with excellent high-temperature properties increased, the development speed of silicon nitride ceramics increased significantly. At present, the development of silicon nitride materials is focusing on the ceramics and electronics industries and continues to expand to other application areas.
1. Silicon Nitride Ceramic Bearing
Ceramic bearings have been developed rapidly since they were developed in 1972. It has been widely used in precision machine tools, automobiles, aero engines, chemical instruments, superconducting devices, and other fields. Considered as a bearing material, the most basic characteristic is rolling fatigue life. In order to evaluate the applicability of various ceramic bearings, the rolling life test was carried out with a ceramic plate. The order of rolling life is alumina < silicon carbide < zirconia < nitriding silicon. It can be seen that among the four common engineering structural ceramics mentioned above, Si3N4 is the most suitable for use as a bearing material.
2. Aerospace
In the aerospace field, the requirements for material performance are very demanding, challenging the limits of traditional materials. Si3N4 is a good choice for aerospace applications due to its high temperature strength, good fracture toughness, high hardness, high dielectric strength, excellent thermal shock resistance, and tribological properties, which can ensure excellent mechanical reliability and wear resistance. It can be used as rocket combustion chamber thrusters which are used to control satellite orbits. Because high-temperature combustion can obtain greater propulsion, so it needs the material not only light in weight but also to be able to withstand high temperatures.
3. High temperature parts of automobile engine
The Si3N4 ceramic components used in automobile engines include turbocharger turbine rotors, preheated combustion chambers, rocker arm inserts, injector connecting rods, valve guides, ceramic piston crowns, glow plugs, etc., especially the most difficult ceramic rotor products. Into certain ceramic engines, small turbine rotors have entered commercial scale production
4. Silicon nitride ceramic heat sink substrate
Although the thermal conductivity of silicon nitride ceramics is lower than that of aluminum nitride and beryllium oxide, it is significantly higher than that of general structural ceramics, and can basically meet the heat dissipation requirements of the substrate; moreover, the strength and fracture toughness of silicon nitride ceramics are much higher than others. The substrate-type ceramics, which are heat-dissipating substrate materials with excellent comprehensive performance, have been practically used in the electronic control systems of high-speed railways and electric vehicles.
In short, as a structural ceramic material with the most excellent comprehensive performance, many application directions of silicon nitride ceramic have attracted the attention of industry and laboratories. It is believed that with its unique properties, there is still broad room for silicon nitride of development in the future.