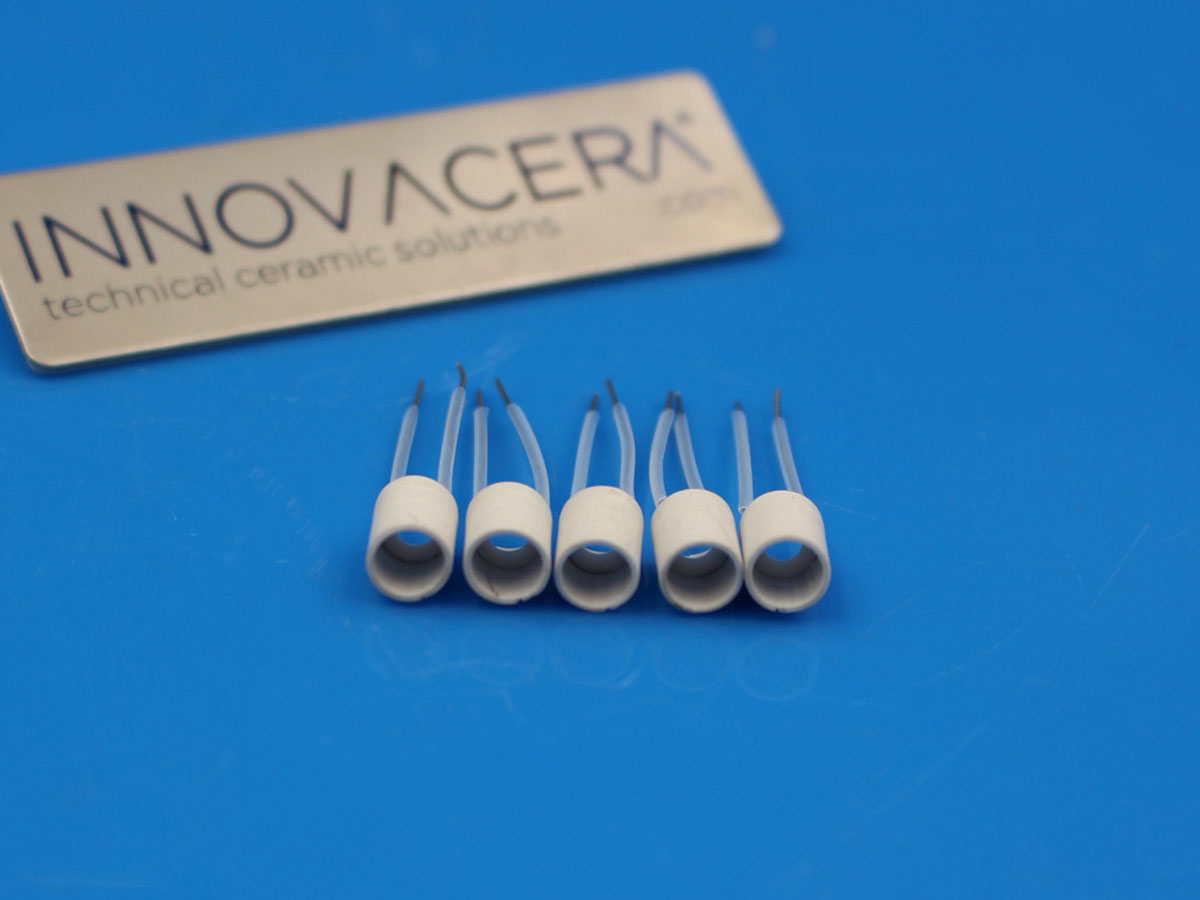
3D printing can be enjoyable when everything is going right. However, it can rack your brains when something goes wrong. 3D printing issues can usually be fixed by adjusting the settings or the parts. But if you’ve tried everything and it’s still not working, it could be that you need to replace a part in your 3D printer, particularly the nozzle.
What could wear out your nozzle? Here are the following reasons:
Nozzle Damaging Practises
Using abrasive filaments
Some 3D printer filaments are tough on regular nozzles. These are usually “composites” or filaments that have been reinforced by fibers to improve their mechanical properties. These filaments are:
- Carbon fiber
- Fiberglass
- Nylon
- Metal-filled filaments
- Glow-in-the-dark filaments
Use tougher nozzles made of hardened steel, ruby, tungsten, and stainless steel when using these filaments. They are much more capable of withstanding the abrasiveness of these filaments and lasting longer than the regular brass ones.
Aggressive nozzle unclogging methods
While unclogging your nozzle can be good for your nozzle and the quality of your print outcome, doing it often and aggressively can wear out your nozzle. You have to be careful of clearing it, using gentle methods and materials to clean it with. Follow our nozzle unclogging and cleaning tips that won’t harm your nozzles.
3D Printing Issues that may be caused by nozzle damage
You may encounter a reduction in print quality when your nozzle is worn out. You’ll notice some of these issues crop up:
- Under-extrusion
- Poor layer adhesion
- Print blobs
- Uneven or rough print surface
However, it can be tricky to attribute these issues to nozzle wear. These issues can also be caused by the following:
- Clogged nozzle
- Setting the bed too high
- Incorrect nozzle diameter setting in the slicer
Check your 3D printer to make sure that you’re not committing any of the mistakes above. If you’re still experiencing the same print quality issues after checking your 3D printer, then it means it’s time to replace your nozzle.
Signs of Nozzle Damage
To the untrained eye, a worn-out 3D printer nozzle looks just like any. However, if you look closely, you’ll see the signs of wear and tear. Here’s what you need to look out for:
- Marks and grooves in the inner walls near the opening
- Bigger nozzle diameter than usual
- Nozzle tip has become dulled down or shortened
Take care of your 3D printer nozzle before it’s too late!
It’s not the end of the world if you have to replace your 3D printer nozzle. They are usually reasonably priced and easy to replace. In fact, it could be smart to stock up on nozzles of different diameters and make since you need to change them depending on the filament you’ll be using and the model you’ll be creating.
INNOVACERA supplies custom Ceramic heating elements for 3D Printer Extruder Hot Ends.
Contact us today with your requirements and our sales engineers will work with you to provide the correct product to meet your application.