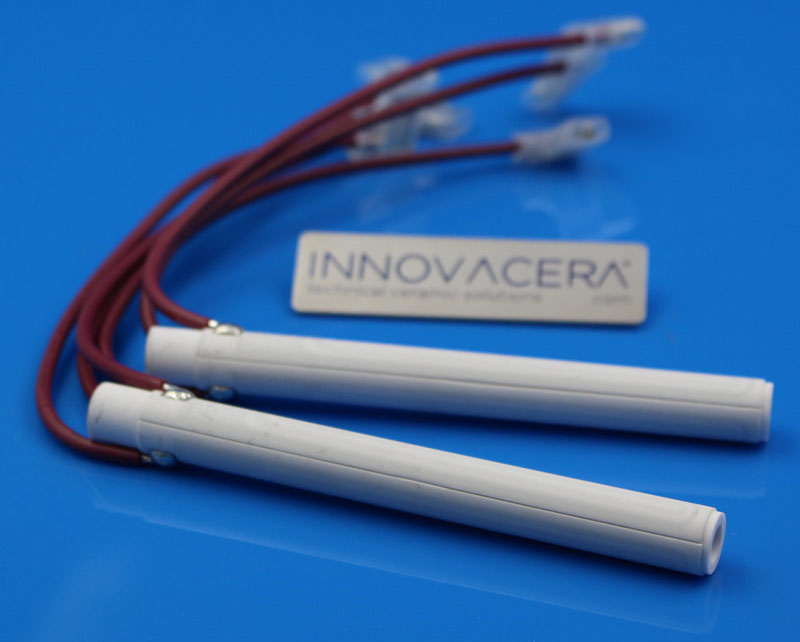
In our daily life, we often encounter the application scenario of liquid heating, and there are various types of heating elements in the process of choosing, with different performance and advantages. Here focus and talk about the ceramic heating tube in the process of water heating whether the fracture will continue to lead to electricity leakage such an unsafe phenomenon.
Ceramic heating tube is made of alumina flow-casting porcelain as insulation layer and substrate, and high temperature metal thick film paste is printed on the raw porcelain side, and then rolled, sintered at high temperature in hydrogen furnace to become a heating element, and finally welded leads to form MCH heating element. Accordingly, besides lead outside, the calorific area of the tube is complete insulation, this contacts to the home appliance with water, if regard water heater as, having an outstanding advantage, the safe problem is ensured.
However, the ceramic heating tube is more fragile than other materials, easy to fracture by a violent impact. Therefore, many customers are worried about whether there will be electric leakage and other unsafe phenomena after ceramic pipe fracture. Do not worry, because of the particularity of the ceramic electric heating tube heating line, after the fracture of the electric heating tube, it will immediately stop the power operation, can completely avoid leakage and other safety hazards, which is more conducive to the application of water heating.
In addition, the ceramic heating tube has another advantage compared with other heating materials, that is, it can effectively reduce the residual scale when water heating. Many water heating products, such as electric kettles and cups, are plagued by scale problems. If metal is used as the heating element, the residue of scale will directly affect the function of the metal tube, life and so on.
INNOVACERA has been in the heating pipe business for more than 10 years. We can design the heating pipe according to the customer’s drawings (voltage, power, size) or by our technical staff according to your requirements. Please feel free to contact us if you need anything