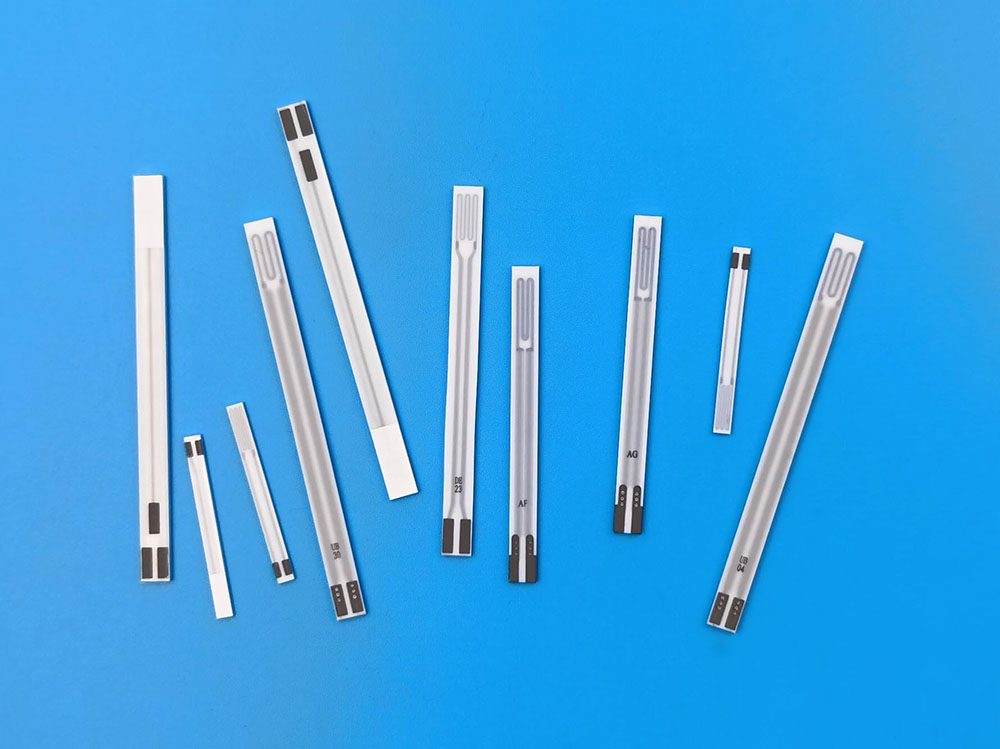
With the development of the automobile industry, especially the increase in the number of automobiles and the frequency of use, the pollution caused by automobile exhaust has attracted more and more attention. Traditional carburetor-type vehicles have not adapted to the new automobile exhaust emission requirements. In this case, electronically controlled fuel injection vehicles have become the mainstream of the development of the automotive industry. The electronically controlled fuel injection adopts a closed-loop control system, which can adjust the fuel injection volume in time according to the different working conditions and emission factors of the engine so that the air-fuel ratio can be maintained at 14.7:1, thereby obtaining ideal power and economy. The oxygen sensor is an important component of the automotive engine electronic control system (EMS)
The role of the oxygen sensor on the car is to measure the oxygen content in the exhaust after the engine burns, and convert the oxygen content into a voltage signal and transmit it to the EMS. Under closed-loop control conditions, the EMS adjusts the engine to make the air to fuel ratio at 14.7:1. Nearby, ensure that the three-way catalytic converter has the greatest conversion efficiency for the three pollutants of hydrocarbons (HC), carbon monoxide (C0), and nitrogen oxides (NOx) in the exhaust gas, which maximizes energy saving and emission reduction Effect.
What types of oxygen sensors are available on the market?
According to the working principle of the oxygen sensor sensitive element, it is mainly divided into: switch type oxygen sensor (concentration type), limiting current type oxygen sensor, and semiconductor resistance type oxygen sensor (TiO2 type oxygen sensor)
Type |
Switch type oxygen sensor |
Limit current type oxygen sensor |
Semiconductor resistance type oxygen sensor |
Principle |
Determine the electric potential based on the difference in oxygen concentration |
Determine the limiting current based on the diffusion of oxygen |
Determine the resistance based on the chemical reaction of the semiconductor surface |
output signal |
voltage signal |
current signal |
Resistance signal |
A/F control range |
Narrow range, generally around 14.7 |
Wide range, generally between 10~23 |
/ |
Examples of market products |
Bosch: LSH/LSF
Denso: O2 oxygen sensor |
Bosch: LSU (Five-line wide domain)
Denso: A/F oxygen sensor |
/ |
Related concepts and characteristic curves
Theoretical air-fuel ratio: A/F=14.7:1 (λ=1)
Rich mixture: When the actual air-fuel ratio is less than the theoretical air-fuel ratio, the mixture is called rich (λ<1).
Lean mixture: When the actual air-fuel ratio is greater than the theoretical air-fuel ratio, the mixture is called lean mixture (λ>1).
When the mixture becomes rich, that is, the concentration of oxygen in the exhaust decreases (λ<1), the output voltage signal of the oxygen sensor is close to 1V.
When the mixture becomes leaner, that is, the concentration of oxygen in the exhaust increases (λ>1), the output voltage signal of the oxygen sensor will be close to 0V.
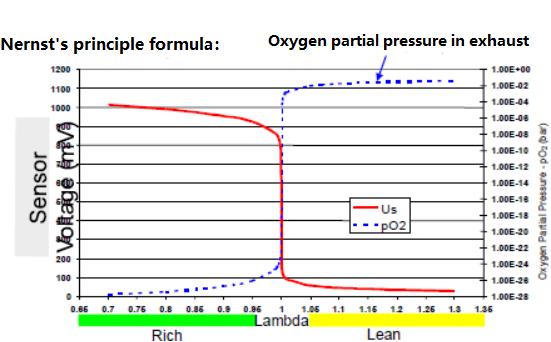
Working principle
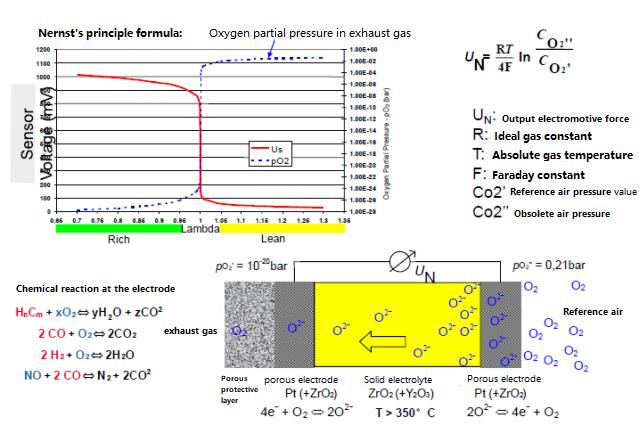
The crystal structure of ZrO2 material
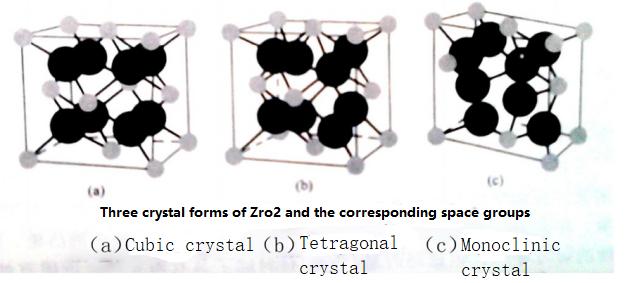
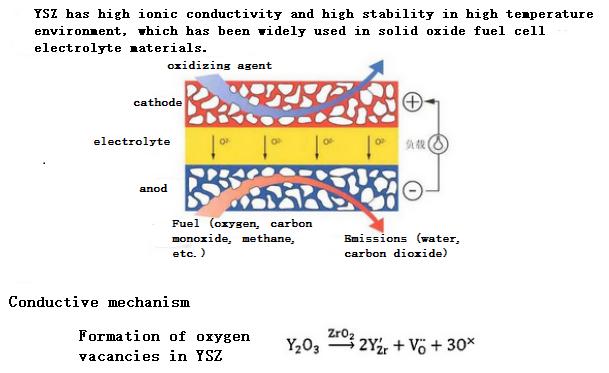
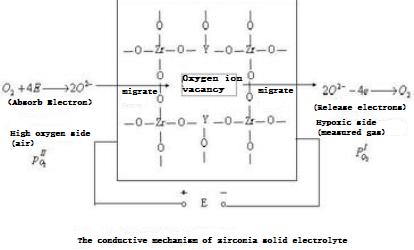
In order to better meet the needs of market development, INNOVACER has now stably supplied the following planar oxygen sensor heating elements. It has a new design that promotes faster heating of the probe. Beginning the monitoring much faster than the thimble type.
1, Typical structure of switch type oxygen sensor sensitive element
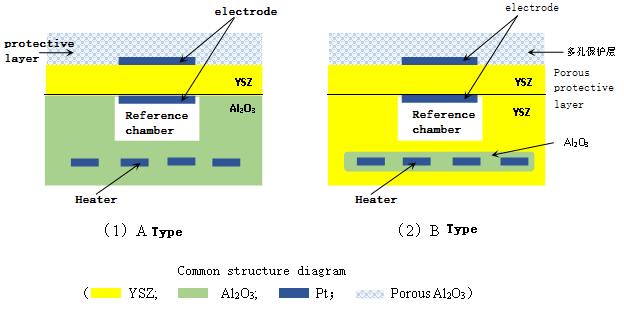
Advantages and disadvantages
|
A type (alumina type) |
B Type (Zirconium Oxide Type) |
Advantages |
1) Good insulation
2) Fast heat conduction
3) Simple preparation process |
1) The base material is the same, and the mechanical strength is higher.
2) The material is easy to prepare |
Disadvantage |
1) The product has a certain curve
2) *Need to solve the problem of co-firing of different materials |
1) Poor insulation reliability
2) Heat conduction is slow
3) The preparation process of the insulating layer is complicated |
* Is the core technology of our company.
2, Concentration Oxygen Sensor
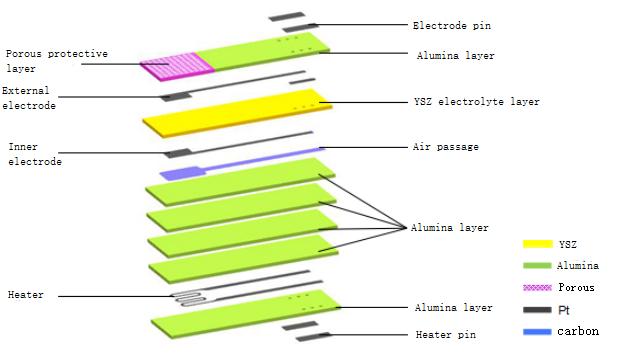
(Schematic diagram of HF sensing element)
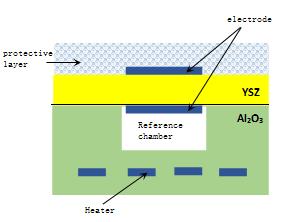

If you have any needs or problems with car oxygen sensors, please feel free to contact us and we will definitely give you the most professional assistance.